
This filters the exhaust air of every print and also improves build temperature stability. It now includes an integrated Air Manager. The UltiMaker S7 is built on the success of the UltiMaker S5 and its design decisions were heavily based on feedback from customers. Liftedbuild KNIFE.3mf Liftedbuild PULL RING.3mf Liftedbuild CYLINDER.3mf Putting them down thinner also allows the interface to cool faster and so the "real" model doesn't tend to stick to the interface as well. I generally run them at 90% to make the supports weaker and easier to remove. One last comment.Your Support Flow and Support Interface Flow at 125% is really high.
#Ultimaker cura 3d skin#
You don't have to do any of that of course, it's just another way to skin this cat. That part does have a couple of features around the base that really could use support, but they are so small that the support can't get in there. With the "Floor Distance" at 2X layer height the scarring from the support won't be as bad. I think it will just print better than way. The one in the attached project file was repaired with MS 3D Builder.) (BTW the cylinder had errors in the model. The vertical orientation will allow those fine features around the cylinder to have much better definition. Bed slinger printers can be rough on tall narrow objects so slowing down the accel on the Y axis softens the moves and keeps the print from being shaken loose and failing. I added some horizontal expansion to the support so the tip would be supported.īecause the cylinder object is so tall I've used "Search and Replace" to change the Y acceleration at layer 650. Each of those models really have different needs so I separated them each to their own file.įor the "knife" file I've done as AHoeben suggests and fixed the Support. I've attached the project file here as well as a few screenshots, and I'm taking a break from trying to figure this out for now. I'm unsure of what to do here, as most of the builds I'm interested in making require a complete round surface and it's just not feasible to print them on another side that's flat (if they even have one). I've tried using a raft, didn't fix it, and I have the drop models setting unchecked for all of the pieces as well as in my preferences.

I've raised the model parts in this project file to a ridiculous height in an attempt to get it to lift it at all to where it's no longer clipping the bottom of the model. I'm using an Ender 3 v2 printer from creality. I *know* the settings are wrong on this, due to both being new at 3d printing and to my attempts to get this working at all.
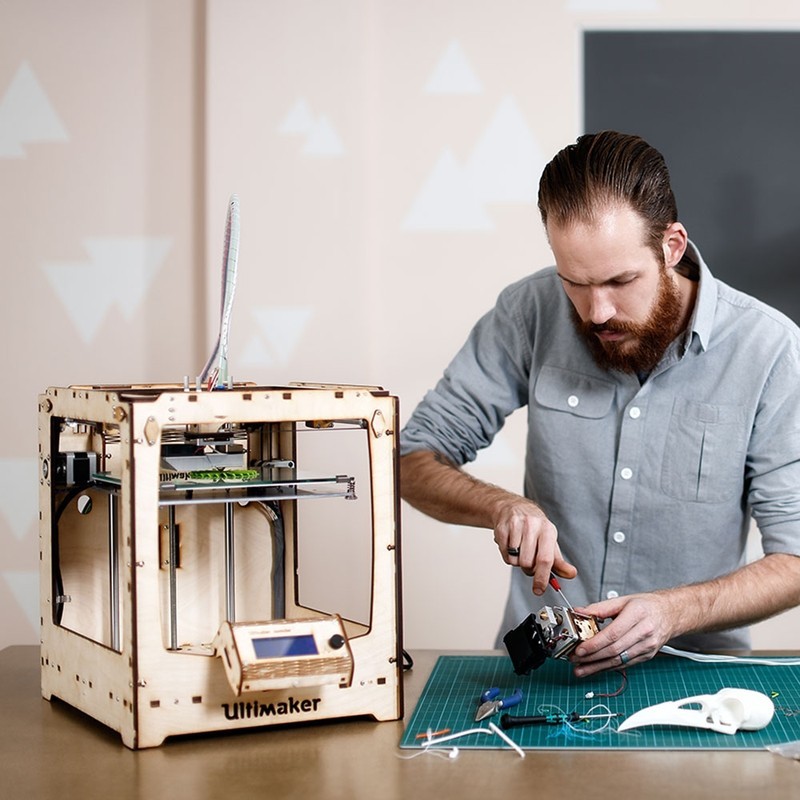
However, the models seem to be clipping below the build plate, causing any rounded edge to become entirely flat on the bottom part. I'm new to 3d modeling/printing and grabbed a few things from thingiverse to print for myself.
